Polished Concrete in Bendigo: Why Is It Popular?
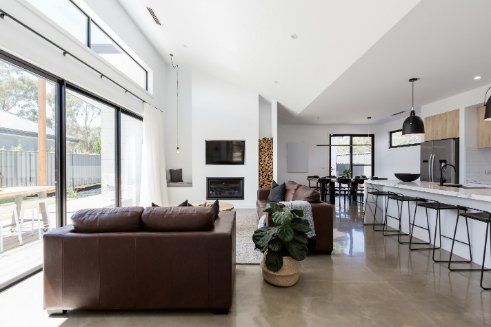
Polished concrete is durable and aesthetics! If you want to turn your concrete floors into stunning, long-term masterpieces, read this article before deciding. Polished concrete floors have become an increasingly popular choice for residential and commercial properties, offering numerous benefits beyond conventional flooring solutions. Polished concrete floors in Bendigo, Victoria, have become an ideal way to achieve glossy floors while ensuring low maintenance costs and long-term durability. This comprehensive guide will explore its unique advantages as a solution for floor enhancement, polishing process details and why polished concrete may be right for your home or business.
What Is Polished Concrete and Why Choose is it Popular?
Polished concrete is a specialised flooring technique that involves grinding and polishing concrete surfaces to produce a glossy, satin-like surface that enhances their natural beauty while adding exceptional durability - making it the perfect choice for residential and commercial spaces in Bendigo.
One of the chief advantages of polished concrete flooring is its aesthetic appeal. Its sleek surface and seamless appearance add a sophisticated feel to any space, elevating its overall ambience. Furthermore, polished concrete's low maintenance requirements and long lifespan make it a cost-effective and sustainable flooring option.
Polished concrete floors provide the ideal combination of beauty and functionality, suiting Bendigo's climate perfectly. In commercial spaces like factories or offices, polished concrete offers a durable, heavy-duty solution that improves safety and work environments.
Polishing Process: From Grind to Shine
Achieving polished concrete requires several key steps. Starting with grinding down the surface to remove imperfections, stains or coatings before beginning the polishing processes step-by-step until reaching desired sheen levels.
Polished concrete offers various finishes, from matte surfaces that retain their natural look to high-gloss surfaces that reflect light beautifully. Homeowners and business owners can select one that best satisfies their interior and aesthetic design preferences.
Customisation is one of the hallmarks of polished concrete flooring. By working closely with an experienced concrete team, you can select your level of shine and colour preference and even add decorative elements such as stains to create a unique and visually striking floor surface.
Polished Concrete as the Perfect Flooring Option in Bendigo Floor Solutions
Within Bendigo, polished concrete flooring has become increasingly popular as an option due to several key benefits:
- Polished Concrete Can Handle Central Victoria's Climate. Its durable nature allows it to adapt well to its surrounding climate conditions, making it the ideal solution for hot summers and cold winters. Polished concrete requires little maintenance and simple cleaning - an ideal option for busy homes and commercial spaces with heavy foot traffic.
- Cost-Effectiveness and Longevity. Polished concrete flooring has proven itself as an economical option over time due to its long lifespan and minimal maintenance needs, making it one of the more cost-efficient choices available regarding both long-term cost-effectiveness and longevity. Polished concrete flooring can easily adapt to residential and commercial settings, be it an elegant residential space, an inviting office environment or even bustling factories. It provides the ideal surface that seamlessly adapts to various environments.
Professional Concrete Services for Polishing
Achieving the desired results when polishing concrete requires skill and experience on behalf of your service provider. A professional team ensures every step in the polishing process is carried out accurately and with care for the best results.
Top-quality concrete services in Bendigo specialise in customising solutions tailored specifically to their clients' flooring needs, using cutting-edge technology and techniques for flawless finishes that surpass expectations.
Its Different Types of Polished Concrete and Their Applications
Polished concrete comes in various varieties that are designed for different applications:
- Slabs for New Constructions. If new construction projects require seamless floors with stunning visual appeal, polished concrete slabs may be installed to create visually striking floors.
- Polishing Existing Concrete Surfaces. Existing concrete floors can be transformed into polished floors by resurfacing and polishing to give them new life.
Hire a Professional Polishing Team
Engaging a professional polishing team offers multiple advantages: Onboarding Experience and Advanced Technologies: Skilled teams bring decades of experience with cutting-edge technologies to craft flawless polished concrete finishes.
- Attaining Excellent Results with Professional Workmanship. Hiring a professional team ensures superior craftsmanship, guaranteeing that your polished concrete floor looks amazing while performing optimally.
- Customise Your Polished Concrete With Professional Guidance. By working closely with experts, you can explore various design options and select a finish that complements your style and needs.
- Polished Concrete as Flooring for Commercial and Industrial Spaces. Polished concrete flooring is an excellent option for both commercial and industrial spaces: it can help keep floors clean while maintaining low maintenance costs.
- Polished Concrete Flooring in Factories and Offices. Polished concrete floors provide a clean and dust-free working environment, improving air quality and creating an ideal work atmosphere.
- Polished Concrete Adds Beauty and Value for Businesses. Polished concrete adds beauty and value to commercial spaces, leaving a lasting impression on customers and clients.
- Enhancing Safety With High-Quality Polished Concrete Floors. Polished concrete's slip-resistant properties decrease the risk of accidents in busy commercial settings.
Unleashing the Beauty of Polished Concrete in Bendigo
Polished concrete stands out as an ideal flooring option in Bendigo due to its enduring appeal and practicality. Combining beauty, durability, and low maintenance costs with customisable finishes and designs available via polished concrete allows users to achieve stunning floors tailored to their style and needs.
Contact us today at 03 4420 4768 to know more about our service!
You might also like
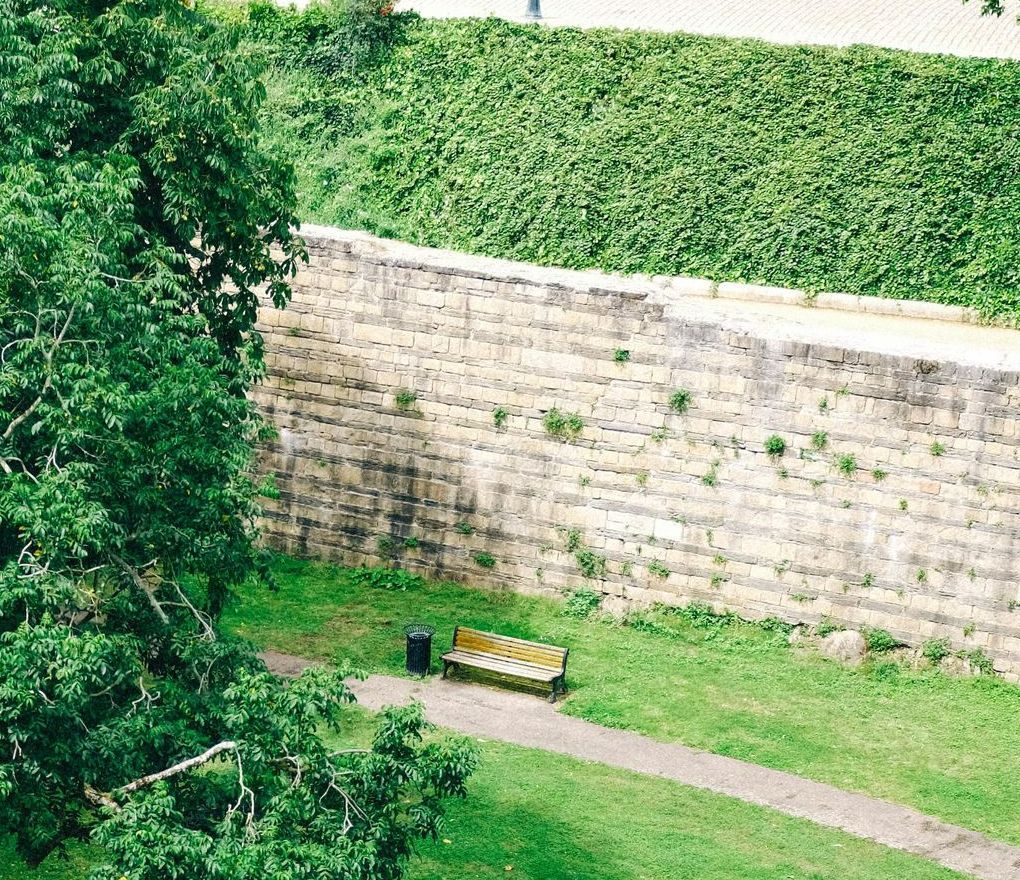
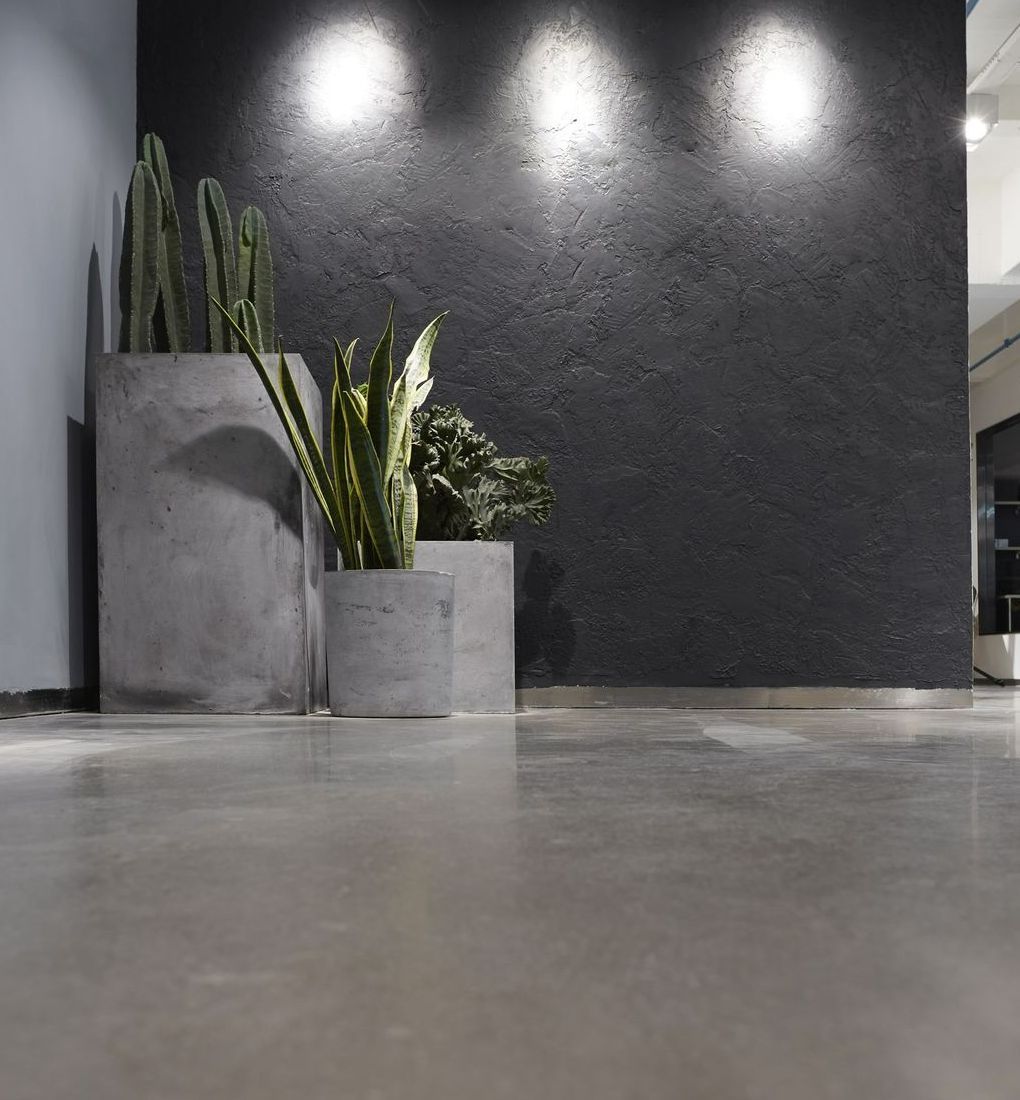
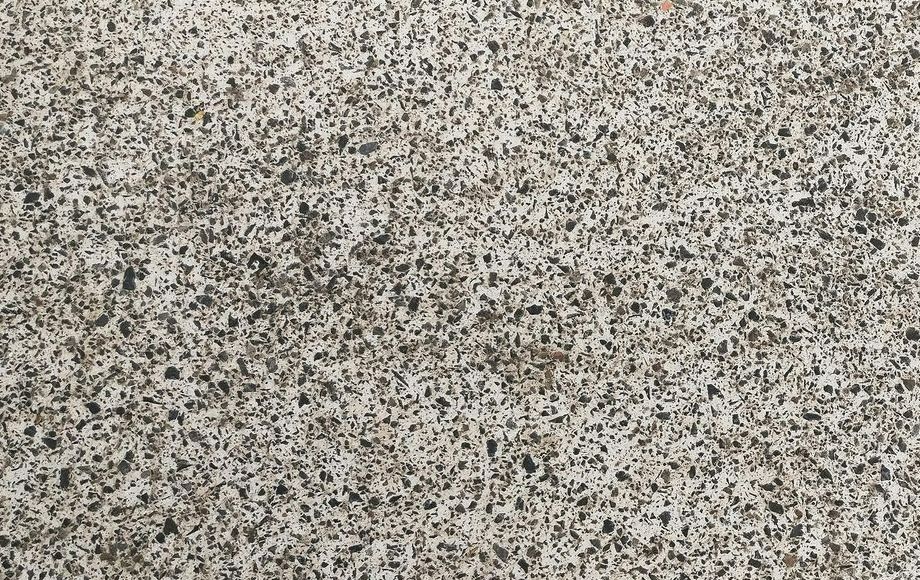
FREE INSTANT QUOTE
**plus free bonus coupon**